Linen story from plant to fabric, raw material to fabric
The life cycle of a flax crop is 100 days,
Condensed the thinking and observation of the grower.
If this fiber has no future, no fiber has a future.
——"Be Linen" CELC
Who am I?
They put me in a hole in the ground,
They take me out of water,
They put me back in water,
They burn my bones,
They dry me,
They beat me,
I serve at a nobleman’s table,
I accompany him from birth to death.
"Raw Material: Seed ~ Fiber"
Where does the best flax grow?
“Attached to the earth but open to the world”, is the connecting thread of linen's European story. From Riga to Belfast, from Courtrai to Venice, from Saint Malo to Cadiz, from Lille to Milan, it influences markets around the globe but is also synonymous with a typical European art of living. 68% of the world's linen fabric production comes from European soil.
From species research and development, the whole process of planting control, the development of agricultural machinery, professional linen technology...from breeding to planting to linen, the cooperation between high-level practitioners has condensed the wisdom and experience of several generations, which has never been Intermittent, making it impossible for other parts of the world to replicate. EUROPEAN FLAX has become synonymous with the world's premier flax fiber production and quality. It has become the world-renowned growers and raw material suppliers such as Terre de lin / The Land of Flax, Albert Brille NV / Pey Group, and has become the strongest reason for our first choice! Starting from EUROPEAN FLAX®, which is fully traceable and certified, we are confident that we will slowly start serving customers with excellent materials and help more consumers enjoy sustainable, traceable, high-quality, innovative and unique flax.
"An ancient seed, the germ of its life is hidden inside, but it needs to be sown in the soil of the new age.
-Tagore
Planting process-from seeds to fibers
Seeds selection
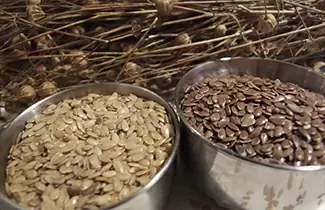
Sowing
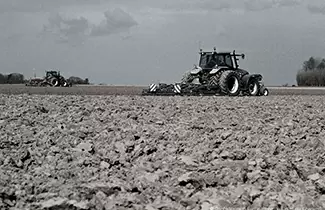
On the world's top flax planting belt, farmers have strict requirements for sowing: follow natural farming methods, and plant approximately 2,000 seeds per square meter on plots with sufficient recuperation and fertile growth after crop rotation.
Flowering (June)
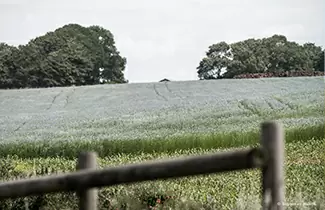
Harvest (July to August)
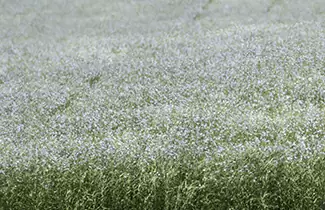
Retting (August)
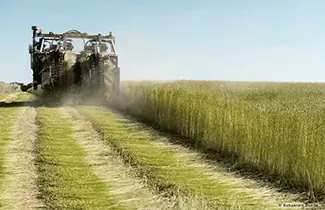
Flap linen
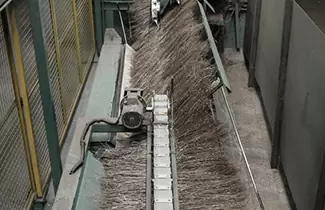
*Mainly based on: natural properties (softness, gloss, density), color, strength, fineness, uniformity, cleanliness and other indicators to comprehensively consider.
Packed in bundles
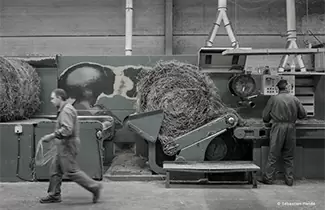
*Reduce the processing time of the carding machine and improve work efficiency.
Spinning process-from flax to yarns
Where is the hope of the world flax industry?
"The hope of the world's flax industry lies in China. China's flax industry can create a new market, which can not only increase the world's flax consumption. But also make noble flax products play a greater role in meeting consumer needs. We believe that China has enough strength to create enough added value to bring the flax industry to the next level."
—— Frederick Duch, President of the European Flax and Linen Federation
Leaving the magical land of Normandy, with the identity of EUROPEAN FLAX®, most of them were sent to China. Started another life journey that has undergone magical transformation. Such an excellent fiber raw material, whether it is fiber length, splitting degree, and strength, is the best. The color uniformity is also due to other linen producing areas, so it is not difficult to understand that our yarns are both in appearance and internal physical properties. So different. Of course, this will inevitably be inseparable from our long-term partners Jinda Holdings, Golden Eagle Group and other companies in terms of processing and textile experience, continuous innovation and environmental protection efforts. Only by making it stronger (up to 2 times that of cotton and 3 times that of wool) can it be woven into a cleaner and durable fabric. As time goes by, more technical research results make it more valuable.
-
Raw material inspection
When the raw materials enter the factory, experienced workers will conduct strict inspections on the fineness, uniformity and parallelism of each bundle of imported linen, aiming to provide perfect materials for the subsequent process;
-
sorting
Unwrap the linen bundles, then place the linen bundles in rows on the ground, sort them according to their quality, and send them to the wooden corrugated board in the humidification chamber to start the baptism process of humidification and health preservation;
-
Health
The moisture regain of the flax fiber is low, the flexibility is insufficient, and it cannot be carded and spun directly. By layering and humidifying the linen, the top is covered, and the bottom is ventilated for health, so that it is stacked for 18 to 24 hours for health. Excellent health care improves fiber strength and softness, prevents excessive breakage in the subsequent carding, increases fiber length, and improves linen production rate.
-
Beam splitting
Divide the beaten linen into small bundles of a certain diameter and weight, keep the diameter in the range of 2.6-2.8cm, pick out ultra-short fibers, linen, linen chips and other debris according to color and length to keep the fiber pure and uniform. Make the quality more stable;
-
Comb
After dividing the bundles, they need to be combed in a comb comber, separated into finer craft fibers, and combed into longer and stronger linen strips. The finer the linen fibers, the more they can meet the requirements of high-quality textiles. The combed flax is softer, tougher, and lustrous. All this is inseparable from experienced workers. From the consistency of the linen bundle in the linen holder to the timely selection of the uncombed linen, the passion and experience are the The guarantee of the birth of high-quality linen.
-
Into strips
If combing long flax to turn into spun yarn perfectly, the quality is the key! In addition to imported sliver machining, experienced and dedicated workers have become the guarantee for the continuous and uniform structure of long linen slivers of fine chemical fibers;
-
Draw
Combine the linen sliver to improve the unevenness of the long segments of the linen sliver, so that the thick and thin sections of the sliver have a chance to overlap with each other, and use the drafting method to further split and comb the linen sliver to split into finer craft fibers. Only by combing out small impurities and removing some short fibers can we leave the high quality long linen fiber we need;
-
Roving
Flax spinning is more difficult than cotton spinning. The molecular arrangement of flax cellulose is more linear, relying on accompanying organisms to stick together, unlike cotton cellulose, which can be helically entangled. Spinning linen requires experience. It not only requires pure mechanical processing of the fiber without adding chemicals and no spinning oil, but also with the help of a unique wet spinning process to adapt to the moisture regain and strength of the flax fiber in the wet. The proper twist becomes a flax roving;
-
Boil and bleach
Both short linen roving and long linen roving need to be scoured and bleached to enter the next wet spinning process. The five-step process of pickling, sub-bleaching, water washing, oxygen bleaching, and water washing is used to deeply remove residual lignin and pectin. Spinning, increase the degree of fiber splitting, increase the fiber strength of the roving, and reduce the rate of spun yarn breakage;
-
Spun yarn
As one of the most important processes of flax yarn, high-quality flax yarn is a perfect combination of advanced equipment, leading technology and rich experience. Our partners are based on intelligent spinning equipment, modern management, and intelligent blessing. Under the three major functions of drafting, twisting, and winding, flax yarn greatly reduces end breaks and defects. It is predicted that the strength of a certain section of the yarn is unstable, and the laser automatically cuts it, and then undergoes an excellent splicing process to ensure the tenacity and strength of the yarn, and also makes the later linen more durable;
-
drying
The linen yarn from the wet spinning machine is rich in moisture and is not conducive to storage, so it needs to go through drying to remove the excess moisture, presenting a perfect wet and dry form, which is convenient for storage and smoothness of the next process;
-
Color separation
After drying, the spun yarns are finely screened by the yarn selector. The yarn ears of the same color are gathered under the same count. After the yarn selection is completed, the information label, count, public number, duty and The number of bobbins, etc. Separation is not only a sharp eye, but also good care of flax yarn;
-
Doffing
The dried spun yarn bobbin is re-wound onto the bobbin to form a bobbin with a larger capacity, which is convenient for sale, transportation and storage;
-
Test
Inspection workers use advanced equipment to measure the quality data of the yarn and compare it with the international count standard to determine whether it is qualified. Qualified yarn branches are placed and labeled in order of color and grade to ensure traceability;
-
Package
The yarns that meet the standards are packaged with a packaging machine, put into the packing bag one by one, sealed, and finally packed and weighed into the warehouse, and the information is registered for easy sales and transportation;
The rough and messy linen, through multiple mechanized processing and strict quality control, has become an ingot of fine hair, pure white and holy art. It condenses our important partners Jinda Holdings, Golden Eagle Group, Changzhou Meiyuan and other powerful brands for ten years of continuous pursuit of high standards, helping us to lay a solid foundation for the quality of our fabrics.
Weaving process-from yarn to greige
Excellent linen fabrics will make people feel more heart-pounded, that soft and waxy hand feel, with the touch of nature. We have an intimate relationship with a living material like flax over time. From one ingot to one horse, every process and every link is our memory of the habits of flax fiber. From the warping, sizing to the machine, we choose the best Italian rapier looms to be gentle, and finally show in the texture and appearance, so that the linen grey fabric can live up to the glory of the queen of natural fibers.
"I like linen because it is a noble fabric with unlimited possibilities."
-Giorgio Armani
-
Yarn inspection
For those exciting fabrics, yarn is a new starting point. Therefore, at the beginning of the yarn entering the factory, it must undergo strict inspections, from the appearance and re-inspection of the MIL-STD-105E standard, to the average value of the internal quality strict compliance with the national standard sampling inspection, yarn twist, twist direction, structure As well as breaking force and elongation, each index determines the texture of the subsequent fabric, so it will be reviewed level by level and checked at each level;
-
Sizing
Sizing is a necessary process and technology before weaving. The warp yarn passes through the sizing liquid, and then is pressed, dried, and wound into a weaving shaft. Even if it is finished, the warp yarn is smoother and tougher after sizing, which greatly reduces the yarn breakage rate on the loom;
-
Warping
The warp yarns of a certain number and length are drawn from the winding spool to form a yarn sheet, so that the warp yarns have uniform tension, and are closely wound parallel to each other on the warping shaft, making preliminary preparations for forming the weaving shaft;
-
Reed
The reeding process needs to be done manually. The conventional number of warp yarns is 3000-4000. Workers need to pay great patience to thread the single linen yarn into the reed one by one;
-
Weaving
The yarns that meet the standards are packaged with a packaging machine, put into the packing bag one by one, sealed, and finally packed and weighed into the warehouse, and the information is registered for easy sales and transportation;
-
Test
Because linen yarn has more hairiness and uneven texture, the woven linen may have problems such as linen particles and weaving defects. Therefore, the cloth surface needs to be inspected and then handed over to the repairer to complete the repair. The task of blank inspection is to determine the quality level of the off-machine gray fabric according to certain standards based on physical indicators and appearance defects;
-
Trim
Linen fabric undergoes multiple strict quality inspections of one meter by one meter. If necessary, defects will be repaired by hand to ensure the output of each high-quality fabric;
-
Secondary inspection
After finishing the linen cloth, it still needs to go through about 20 tests such as weight, width, hand feel, oblique weft, color fastness, thickness, etc. The strict four-point system is adopted to ensure the quality of each piece of linen grey cloth;
-
Package
The "grey cloth" woven at this time is jerky and rigid, and cannot be directly applied to the development of clothing and home textiles. However, the embryonic form of linen fabric has emerged, showing different qualities depending on the count and twist. In order to ensure the cleanliness and quality of the grey fabrics, the inspected grey fabrics must be preserved through rolling, packaging, and finally transported to another finishing processing plant.
-
Whether it is fiber processing, spinning, or weaving, we insist on restoring the authentic quality of fiber by mechanical processing, and strive for perfection in every link, and finally the delivery of the next process will have excellent quality. Perhaps it is precisely because of this persistence that we get together with European flax and the world-renowned excellent flax textile suppliers in China to establish intimate relationships with changes in the light and attract more end brands that pursue quality.
Dying&Printing process-from greige to finished
Grey fabrics make our linen fabrics take shape. If we want to meet the demands of customers and consumers in all aspects of aesthetic life, we need to pass the rough grey fabrics through pre-processing, printing and dyeing and post-processing. Every link The quality of the product will be the basis of the next step of the process, so whether it is to remove impurities on the fabric by cooking, scouring, bleaching, etc., or the balance of dyes, process texture and environmental protection in printing and dyeing, or even the final post-processing Superb linen, we strive for 100% completion in every detail.
-
Grey cloth inspection
We are well aware that the lax inspection of grey fabrics is likely to become a disaster for this batch of finished fabrics. Therefore, before we formally enter the dyeing and finishing process, we use the internationally used American four-point system as a guideline to strictly inspect the grey fabrics, reject the grey fabrics below first-class, and pass the fabric turning, batching, printing and sewing processes. Prepare for the next singeing;
-
Singeing
We regard singeing as a grey cloth for washing the face, so we need to grasp the heat, which can completely remove the rough fluff on the surface of the grey cloth, but also must ensure that the fabric is not damaged, so as to obtain a smooth surface, reduce subsequent lint, and cause printing and dyeing defects. Although the quality of ordinary fabrics reaches level 3 is already very good, we always strive for the highest level 4 standards;
-
Cook
Next, we need to take a bath for the linen grey cloth. The main goal of scouring is to help the fiber remove natural and artificial impurities, so that the fabric can be cleaned, so as to achieve the activity of absorbing fuel, so that the color after subsequent dyeing is uniform and the color fastness is high. Lay the foundation. Of course, the use of chemical ingredients is inevitable, and we choose the most environmentally friendly scouring aid that does not harm or pollute the fiber;
-
Bleaching
In addition to natural impurities, grey fabric fibers also contain a certain amount of natural pigments, which directly affect the vividness of dyeing and printing, so it is bleached. In order to ensure the effect and take into account the protection of the environment, we abandon the environmental pollution of sodium chlorite bleaching and replace it with double oxygen bleaching. Not only the whiteness is better, the color is pure, it is not easy to yellow when stored, and it is safer and more environmentally friendly;
-
Mercerized
In order to improve the surface gloss and feel of the fabric, increase the dyeing rate and dimensional stability, the grey fabric before dyeing needs to go through the mercerizing process. Under a certain tension state, with the help of some additives, the grey cloth can maintain the required size, so that the cloth surface has silky luster and reduces the shrinkage rate of the fabric;
-
Dyeing
It is difficult for the uniquely attractive linen fabric to leave the exquisite dyeing process. We are good at presenting the naturalistic linen fabric with high-grade gray texture with the bright and low-saturation environmentally friendly dyeing process, and maintain good color fastness and finish. Combining the individual characteristics required by different customers, the natural color brings out the richer creativity of the dyeing process. Today, when chemical dyes are flooding the global market, we are pursuing color quality while respecting our environment. From the organic dye additives of Italian BOZZETTO to the discharge of a large amount of purified water after dyeing;
-
Stenter setting
The wet fabric has a certain degree of plasticity. In order to make the performance of the finished fabric more stable, it is helpful for designers to develop different styles of clothing or home textiles. The linen needs to be stretched slowly to reach the specified width, and at the same time, it is made under the action of heat. Stable form;
-
Shrink
We make Tumble Dry in strict accordance with American standards, and guarantee that the shrinkage rate of the linen fabric does not exceed 3% after washing 3 times, which has excellent stability;
-
Post-processing
Of course, we will add process expressions such as sanding, mercerizing, air washing, coating, softening agent, stiffening agent, etc. according to the needs of customers for different uses of fabrics to fully meet customer needs;
-
Four-point test
When the linen that looks like a work of art appears in front of us, it needs the last important process to be the product delivered to the customer. This time we still adopt the American four-point system standard, and use experienced and demanding inspection workers to complete the final acceptance to ensure that everything that goes out of our hands is first-class fabric;
-
Package
Next, the qualified linen will be rolled, packaged, stored for easy transportation, and finally delivered to our customers.
-
From plants to fabrics, from raw materials to fabrics, we firmly believe that only the common value concept and long-lasting passion can bring together high-quality European flax raw materials with domestic partners in spinning, weaving, dyeing and finishing. The inheritance of each other's rich knowledge and experience, continuous innovation in the cause, and consistent persistence and tacit understanding of quality can better help more and more customers achieve their dreams. I am grateful to the flax supplier partners who have been working together for more than 10 years and the customers and friends who trust and give us opportunities. Because of you, Runyuan can embrace a broader and better future!
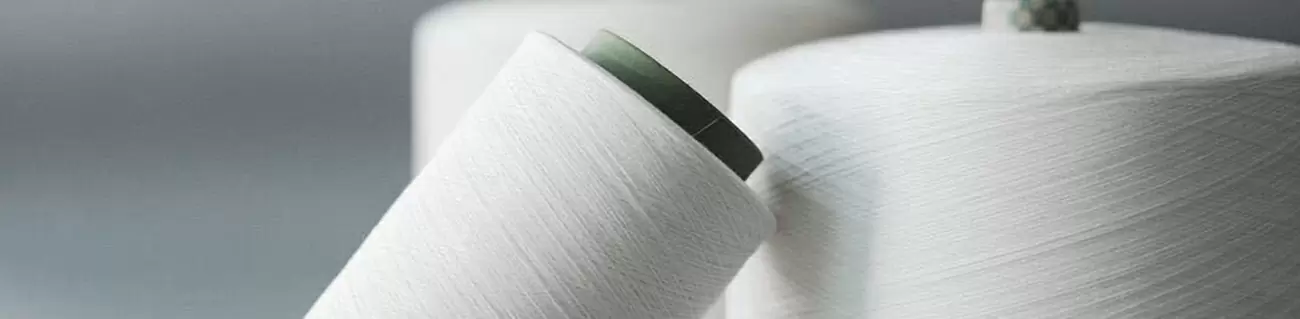